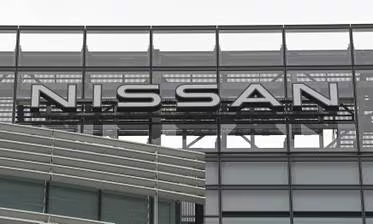
日産自動車は16日、電気自動車(EV)の基本性能を大幅に高める「全固体電池」などの次世代中核部品の概要を明らかにした。全固体電池は「リチウム金属負極」を採用し、従来の車載電池の約1・5~2倍となる1千ワットアワーのエネルギー密度を実現する。また、中国などに偏在し高性能モーター用に需要が拡大しているレアアース(希土類)のネオジムを使わずに高い性能を達成する世界初の「サマリウム鉄系磁石」を導入する。
電池は同じ体積の場合、エネルギー密度が高い方が電力をより長い時間引き出せるため、EVの航続距離性能の向上につながる。リチウム金属負極は、電池材料として一般的に使われる黒鉛に比べてエネルギー密度を高められるが、扱いが難しく、全固体電池の量産に採用するのは日産が初めてとみられる。
リチウム金属負極の全固体電池は正極内のリチウムが充電時に移動して負極に固体として現れ、放電時には正極側に溶解するため、電池が膨張収縮する。
日産はコンパクトな機構で、高い圧力をかけて電池の膨張収縮を制御できる独自の仕組みや、リチウムが負極として均一に現れる作り方などの新たな生産技術を開発。これらによりリチウム金属負極型の課題を解決したという。
全固体電池については既に横浜工場(横浜市神奈川区)で試作生産ラインの建設に着手しており、令和10年度の実用化に向けて来年3月をめどに試作量産を始める予定だ。生産能力はEV「リーフ」用の約2000台に相当する年間100メガワット規模。
一方、次世代の電動駆動システムでは部材の調達リスクの低減とコストの30%削減を目指し、3つの世界初の技術を実用化する。
レアアースの中でも、ネオジムに比べて用途が少なく安価な材料のサマリウムを使い、ネオジム磁石よりコストを30%低減した高性能磁石を開発。さらに、専用設計だった電力制御のパワー半導体を汎用の半導体で、モーターの銅線を、銅より安くて軽いアルミニウムでそれぞれ代替する自動車分野では世界初の技術も導入する。
鄭重声明:本文の著作権は原作者に帰属します。記事の転載は情報の伝達のみを目的としており、投資の助言を構成するものではありません。もし侵害行為があれば、すぐにご連絡ください。修正または削除いたします。ありがとうございます。